Cosmetics have become an essential part of modern life. To meet the growing consumer demand for high-quality and safe products, cosmetic manufacturers continuously improve their production processes. Among these, ensuring a source of pure and clean water is a key factor that directly determines the final quality of the product. Join ATS Water Technology in exploring the technologies and processes for process water treatment in cosmetic production through this article.
1. Importance of Clean Water Treatment in Cosmetic Production
Water is a vital component in many cosmetic products, making up 60–90% of their composition. It is used to dilute and dissolve other ingredients such as foaming agents, humectants, and pH regulators. Therefore, water quality directly affects the safety and effectiveness of cosmetic formulations. If water contains contaminants, microorganisms, or has an unsuitable pH, it can reduce the efficacy of other ingredients and may even cause skin irritation and health issues for users.
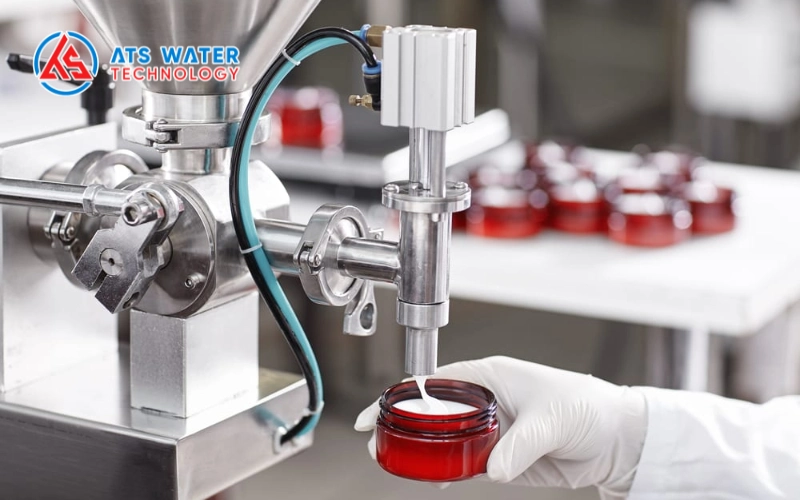
2. Standards for Process Water in Cosmetic Production
Water used in the cosmetics industry must meet strict standards regarding microbiological purity, mineral content, and pH levels to avoid affecting cosmetic ingredients and production processes.
Purified water for cosmetic production must comply with GMP WHO guidelines or the requirements of Pharmacopoeia IV – Vietnam Pharmacopoeia. Below are some key indicators from the Pharmacopoeia IV water standards:
INDICATOR | REQUIREMENT |
---|---|
Appearance | Clear, colorless, odorless, and tasteless liquid. |
Conductivity | Not exceeding 4.3 µS/cm at 20°C. |
Acid-Alkaline Limit | After adding 0.05 ml of methyl red solution (TT) to 10 ml of the sample, the solution must not turn red. After adding 0.1 ml of bromothymol blue solution (TT) to 10 ml of the sample, the solution must not turn blue. |
Ammonium | Not exceeding 0.2 ppm. |
Chloride (Cl⁻) | After adding 1 ml of dilute nitric acid solution (TT) and 0.2 ml of 2% silver nitrate solution (TT) to 10 ml of the sample, no visible change should occur within 15 minutes. |
Nitrate (NO₃⁻) | Not exceeding 0.2 ppm. |
Sulfate (SO₄²⁻) | After adding 0.1 ml of dilute hydrochloric acid solution (TT) and 0.1 ml of 6.1% barium chloride solution (TT) to 10 ml of the sample, no visible change should occur for at least one hour. |
Calcium & Magnesium | After adding 2 ml of ammonium buffer (pH 10.0), 50 mg of Eriochrome Black T mixture (TT), and 0.5 ml of 0.01M sodium edetate solution to 100 ml of the sample, a blue color must appear. |
Heavy Metals | Not exceeding 0.1 ppm. |
Residue After Evaporation | Not exceeding 0.001%. |
Microbial Contamination | The total count of viable aerobic bacteria must not exceed 10² CFU/ml, determined by membrane filtration using casein soy agar medium. |
Bacterial Endotoxins | Not exceeding 0.25 EU/ml. |
3. Advanced Water Treatment Technologies for Cosmetic Production
In recent years, many cosmetic manufacturers have integrated advanced water treatment technologies into their production processes. These solutions ensure optimal water purity for cosmetic manufacturing, including:
3.1. Reverse Osmosis (RO) Technology
RO water is widely used in the formulation of most cosmetic products, including makeup removers, facial cleansers, toners, moisturizers, and sunscreens. In these formulations, RO water acts as a solvent to extract organic compounds from plant-based ingredients.
By utilizing ultra-pure RO water as a solvent, the quality of cosmetic products is significantly enhanced, reducing the risk of skin irritation and adverse reactions.
Additionally, the presence of RO water helps refine product texture, minimize greasiness, and facilitate deeper absorption, ensuring better skin nourishment and protection. As a result, RO water is extensively used in skincare and haircare product manufacturing.
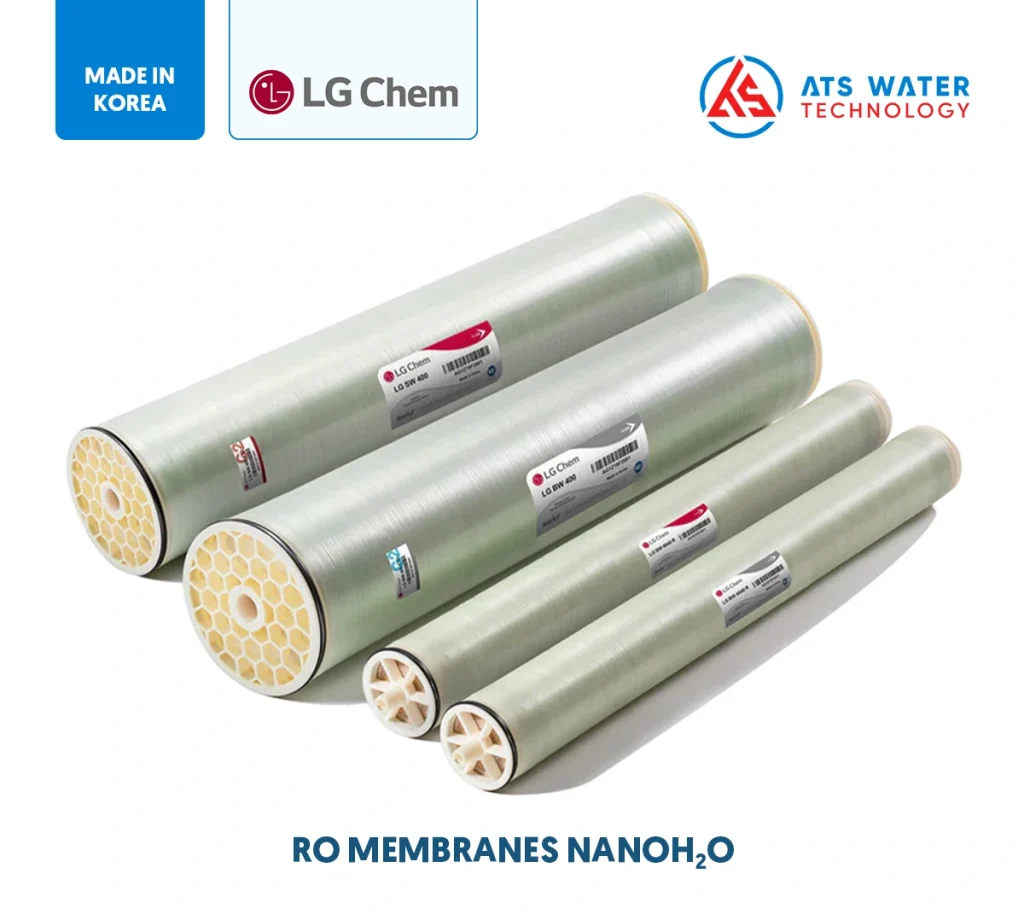
3.2. Ozonation Technology
Ozonation technology is employed to disinfect water using ozone’s strong oxidative properties. When dissolved in water, ozone effectively eliminates bacteria, viruses, and organic contaminants. Compared to chlorine-based disinfection, ozone is not only more effective in eradicating pathogens but also leaves no chemical residues, ensuring product safety. Furthermore, ozone decomposes organic compounds, minimizing the formation of harmful byproducts.
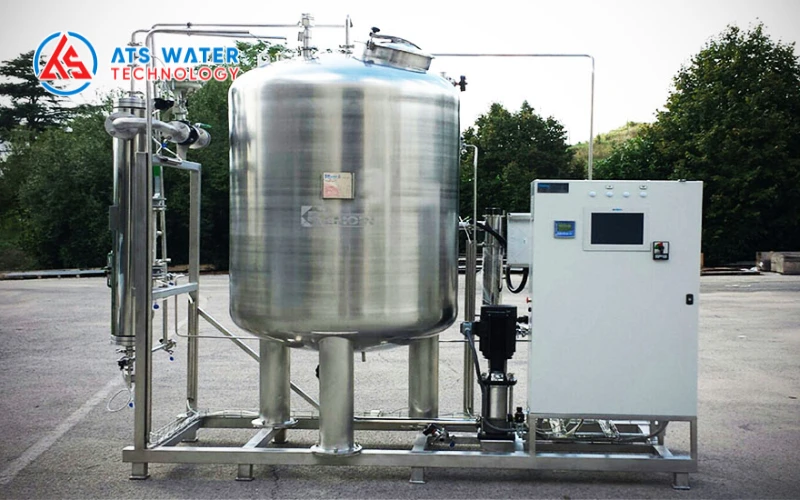
3.3. Activated Carbon Filtration
Activated carbon filtration is one of the most commonly used water treatment methods in the cosmetic industry. Produced from materials such as wood, coal, or coconut shells, activated carbon features a porous structure with a large surface area. As water passes through the carbon layer, organic and inorganic impurities adhere to the carbon surface, removing odors, colors, and pollutants. This method not only enhances water quality but also protects water treatment equipment from damage caused by contaminants.
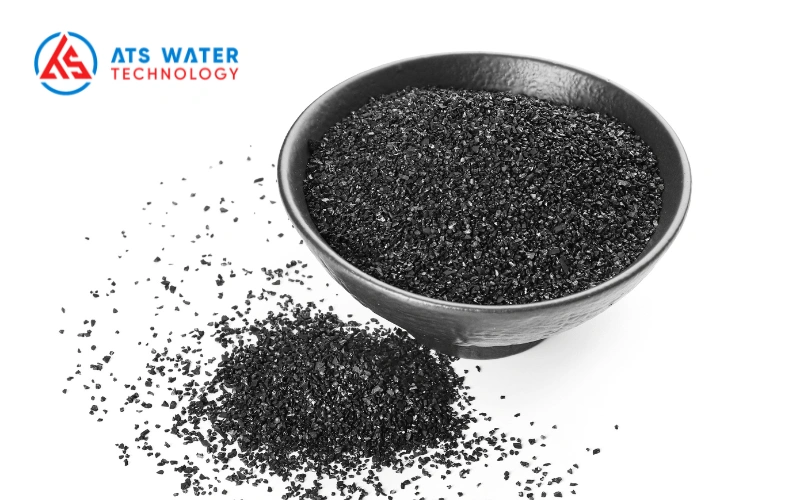
3.4. UV Disinfection Technology
Ultraviolet (UV) disinfection is an advanced and effective method for eliminating microorganisms without the need for chemical additives. UV light sterilizes water by disrupting the DNA structure of bacteria and viruses, preventing their reproduction. This technique not only ensures effective disinfection but also preserves water quality without altering its chemical properties, which is crucial in the cosmetic industry, where water purity and safety are paramount.
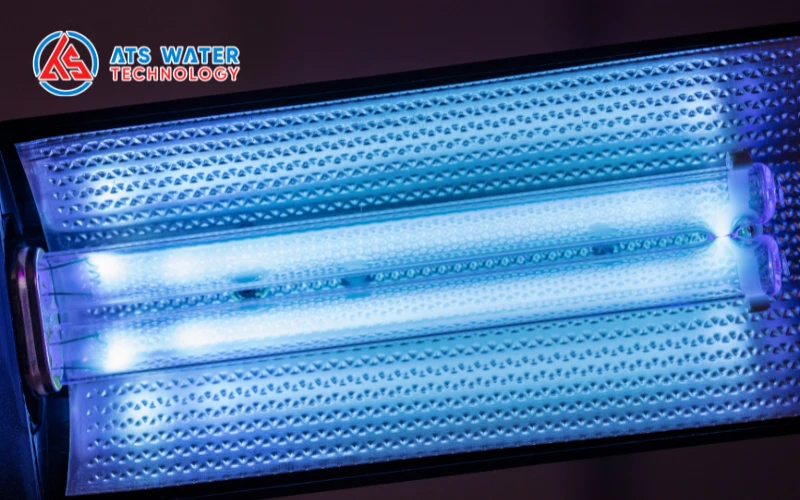
3.5. Electrodeionization (EDI) Technology
EDI technology combines electrolysis and ion exchange to remove dissolved minerals from water. In this process, water passes through ion exchange membranes within an electric field, separating positive and negative ions. The result is ultra-pure water that meets the stringent standards of the cosmetic industry. EDI technology minimizes chemical usage while producing high-resistivity water, ensuring the safety and quality of final cosmetic products.
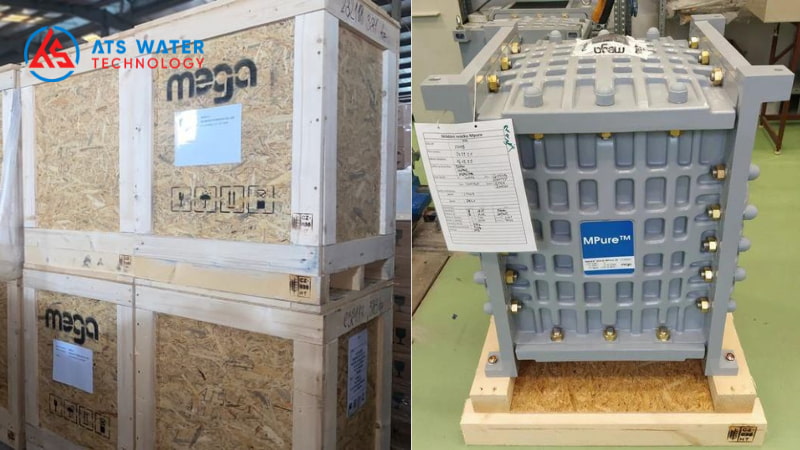
4. Water Treatment Process for Cosmetic Production
The cosmetic industry requires high safety standards for final products, making RO filtration a critical step in the water treatment process. Typically, the RO water treatment system for cosmetic production operates as follows:
4.1. Pre-Treatment Stage
Amiad Self-Cleaning Filter: Raw water is pumped into the Amiad filter with a filtration size of 200–300 µm to remove large suspended solids and protect the downstream ultrafiltration (UF) system.
X-Flow UF Membrane (Pentair): After pre-filtration, water enters the UF system, where X-Flow UF membranes from Pentair, featuring an ‘inside-out’ filtration mechanism and 0.02 µm pore size, remove dirt, bacteria, and suspended particles. The filtered water is stored in a tank, with some directed to the RO system for further purification, while the remainder is used for UF membrane backwashing to maintain stable performance.
Aqualine Fine Filter: Before reaching the high-pressure pump, water passes through a 5 µm Aqualine fine filter to eliminate residual dust particles, protecting both the pump and RO membranes.
PWT Anti-Scaling Agent: A metering pump injects a PWT anti-scaling agent into the RO system to prevent scaling deposits, ensuring membrane longevity and optimal filtration performance. PWT chemicals are NSF/ANSI 60 certified, guaranteeing post-treatment water safety.
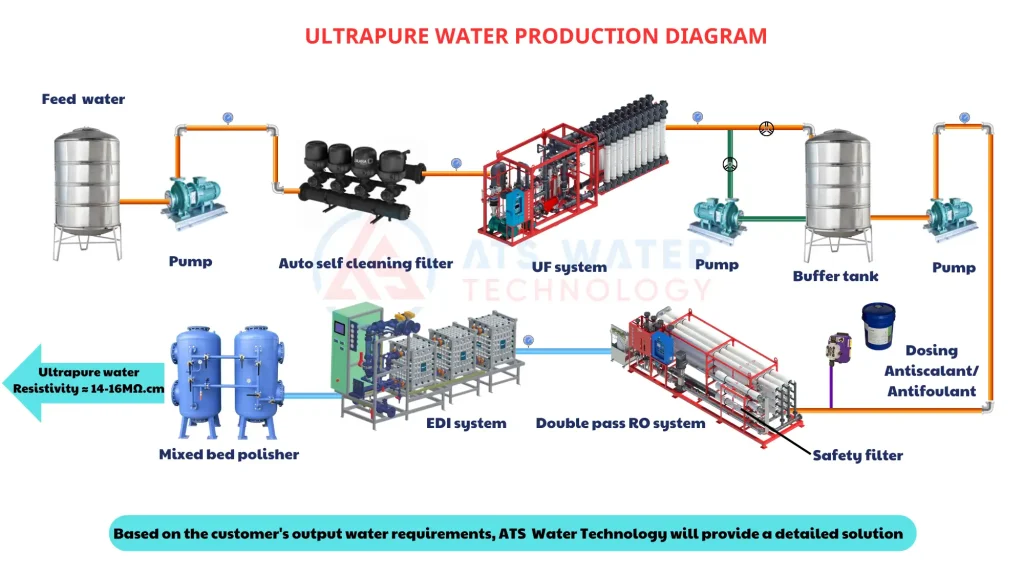
4.2. Main Treatment Stage
NanoH2O RO Membranes: To meet the stringent quality standards of cosmetic water, ATS Water Technology employs LG BW 400 R G2 RO membranes. Utilizing advanced TFN nano-technology, these membranes remove up to 99.8% of salts and contaminants, ensuring the highest purity. Additionally, the low dP Feed Spacer technology minimizes pressure loss, extending membrane lifespan and optimizing system efficiency. The membranes are housed in Codeline Pentair pressure vessels, which provide high-pressure resistance, protect the RO membranes, and reduce the risk of water leakage.
MPure™ Mega EDI Ion Removal Unit: After dual-stage RO purification, water undergoes final treatment using the MPure™ Mega EDI system. By leveraging an electric field and ion-exchange membranes, this system removes nearly all dissolved ions, producing ultra-pure water with a resistivity of up to 18.2 MΩ∙cm.
Note: Source water quality analysis is required to customize system configurations for each cosmetic production facility.
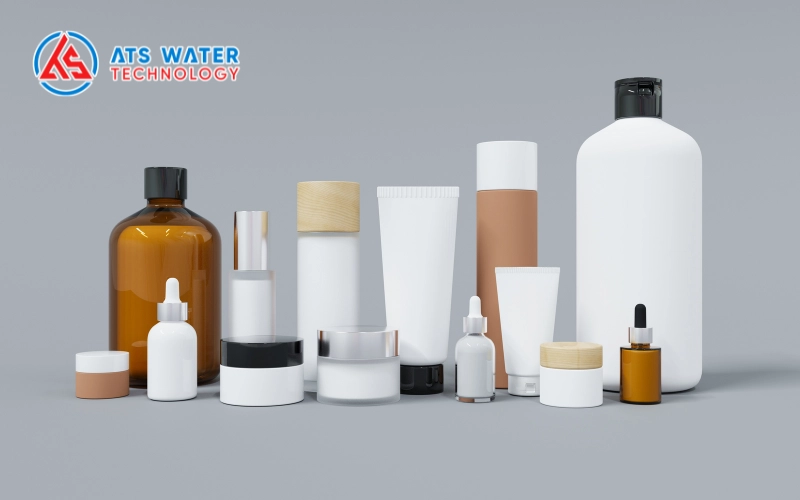
5. Frequently Asked Questions About Water Treatment for Cosmetics
What are the benefits of RO-treated water in cosmetic production?
RO-treated water offers ultra-high purity, minimizing contamination risks during production, reducing skin irritation, and providing an ideal solvent for active ingredients. It plays a crucial role in ensuring the safety, effectiveness, and quality of cosmetic products.
What is the standard water treatment process for cosmetic manufacturing?
The process generally consists of two stages: pre-treatment (coarse filtration) and main treatment (RO filtration and EDI demineralization).
Why is demineralization necessary for cosmetic water treatment?
Demineralization removes ions such as calcium, magnesium, and iron, which can cause scaling and affect product stability, aesthetics, and efficacy.
The adoption of advanced water treatment technologies enhances output water quality, meeting stringent hygiene and safety regulations in cosmetic production. This is an essential trend for cosmetic manufacturers to remain competitive and achieve sustainable growth. We hope this article provides valuable insights into the water treatment process for cosmetic production. ATS Water Technology Co. Ltd is a leading provider of water treatment solutions and equipment in Vietnam. For consultation, please contact us:
ATS WATER TECHNOLOGY CO., LTD
- Headquarter: 54/18 Bui Quang La, Ward 12, Go Vap District, HCMC
- Branch office: 77 DHT10B, Dong Hung Thuan Ward, District 12, HCMC
- Consultation and support: (028) 6258 5368 – (028) 6291 9568
- Email: info@atswatertechnology.com
- Social media: Facebook | LinkedIn | Zalo Official